Today we’d like to share with you a short post with a few pictures of one of our most exciting projects this year.
As you probably know if you follow us online, earlier this year our engineers together with a team of Ubiquo Technologies took part in HACKatHOME. This was a hackathon organized by Xunta de Galicia (local government) to find solutions to fight the first wave of the Coronavirus and we turned out to be the winners of our category (“Low Touch” Solutions). This was of course really exciting for us and it meant the project we’ve been working during the previous months (aka “The Lockdown”) made sense.
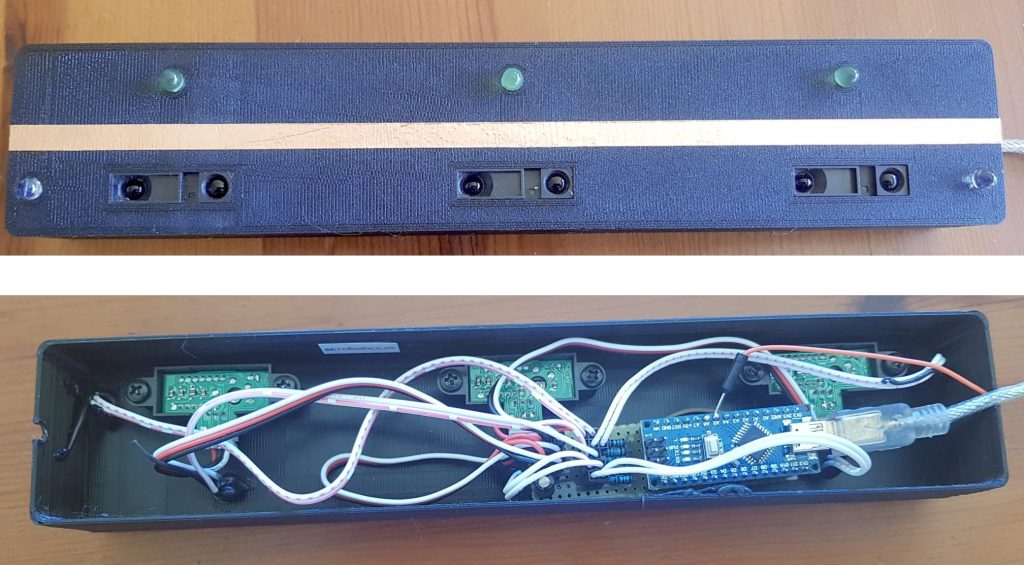
An operator using a touch screen
Of course, this was made with the materials we had at home, but soon we decided to manufacture an MVP we could show. Thanks to 3D printing, a laser cut and a custom PCBA we build our second iteration.
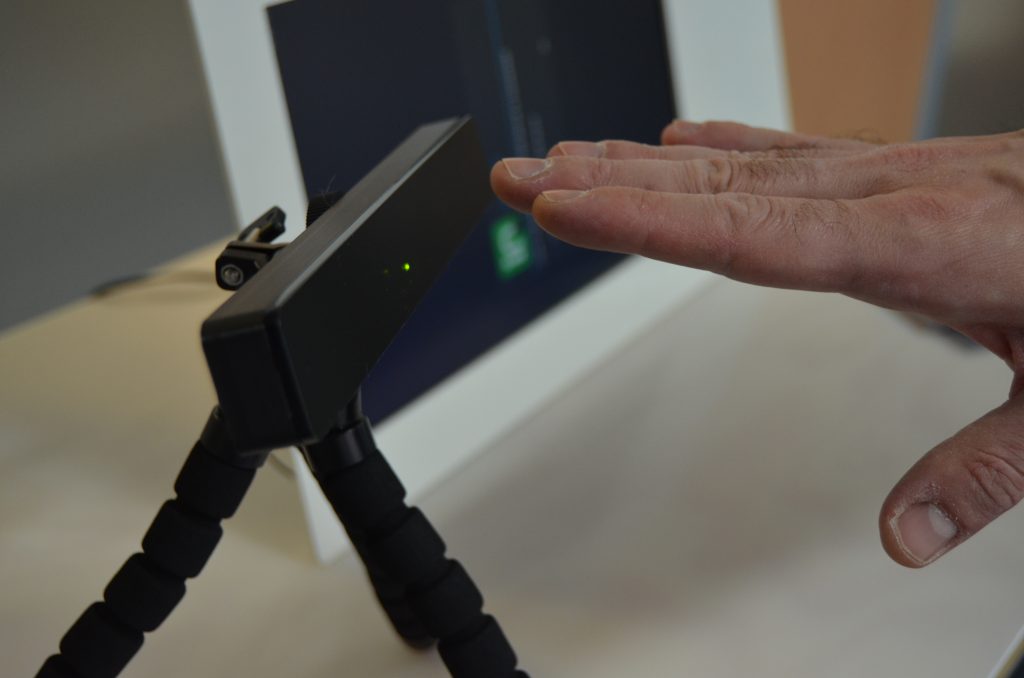
One of the latest versions of the Ntouch Bar on a camera mount
Once we had this device and the virus made it possible, we started visiting clients. One of them was Delikia, quite an important actor in the vending machine market. As it always happens they said something like, “I like it, BUT can you make a keypad instead of a bar?”. And that’s how we started designing and manufacturing the Ntouch Keypads.
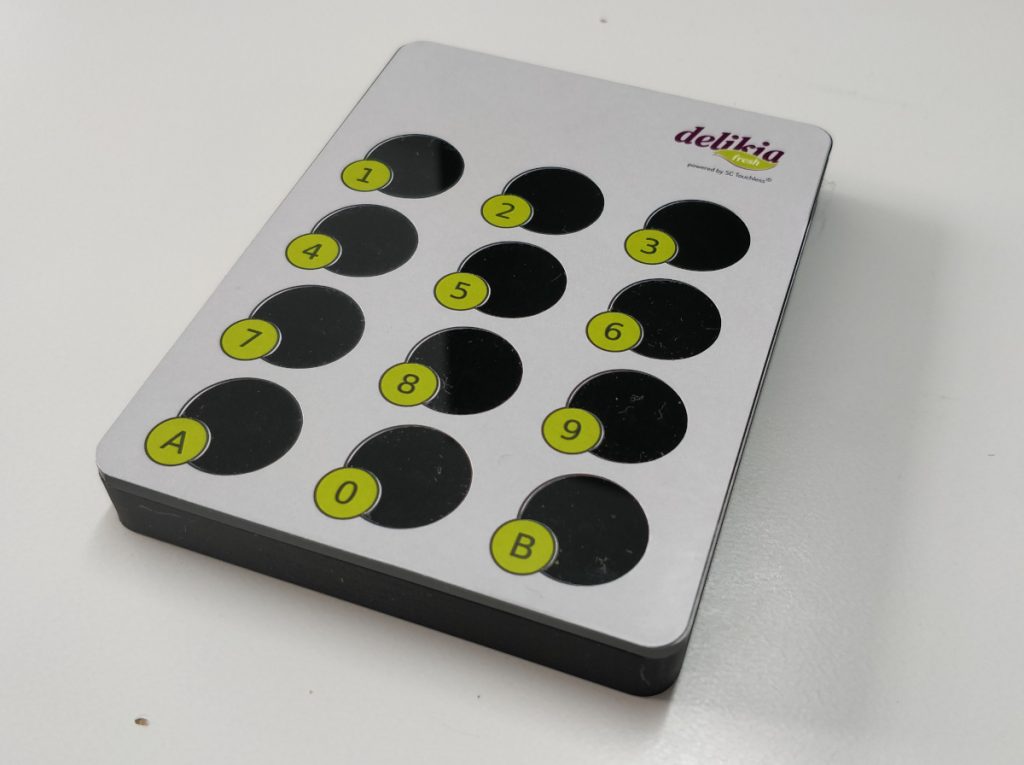
First prototypes of the Ntouch Pad for Delikia
It turns out they liked the device and we started talking about placing a much bigger orders. For us it meant that we couldn’t think about prototypes anymore. Instead we had to consider how to mass manufacture each part of the device.
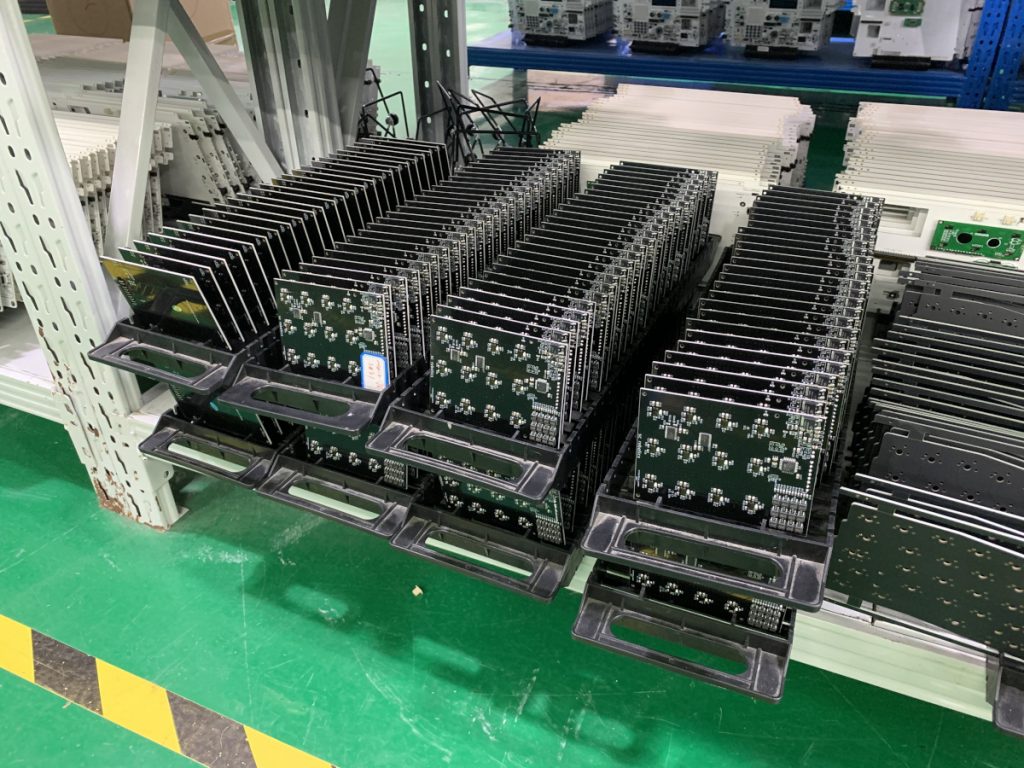

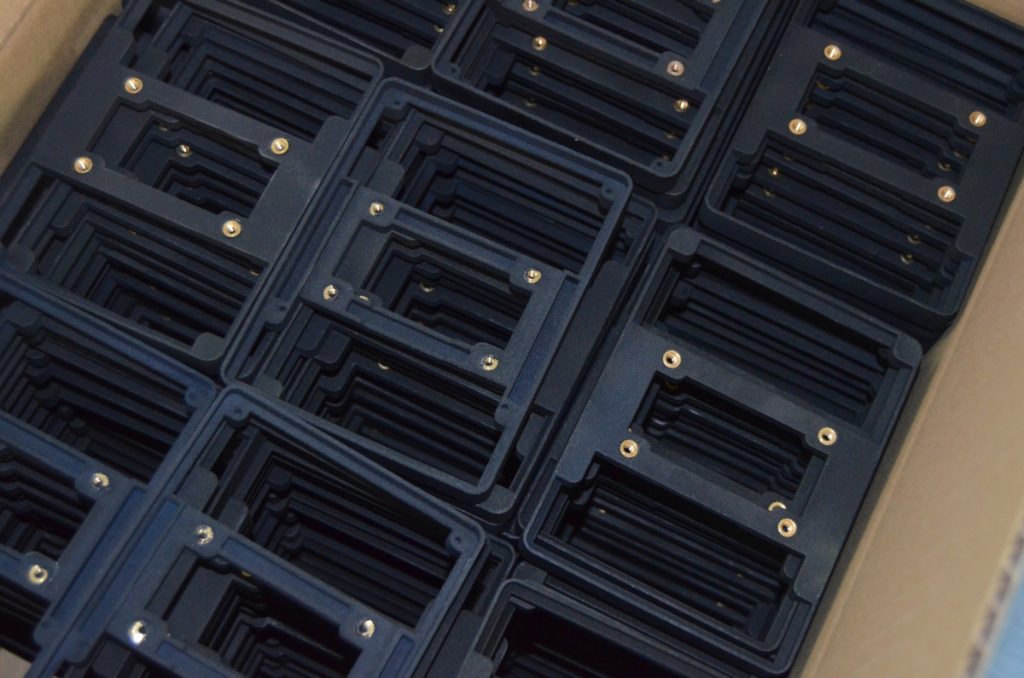
Some of the Ntouch Components ready to be assebled
This was not a big deal, we had to think differently but we could do it (and as it turns out, we did it). The main problem arises during testing, validation and verification phases. When we make 10 devices, it’s quick and easy to validate them 1 by 1, however once you start building tens or hundreds of devices, you might spend more time working on accessory tools rather than on the devices themselves. This was the case. We manufactured jigs for the electronics, designed processes for the assembly, built tools for calibration and so on and so forth. One day we will talk about all these steps in much more detail, but today we just want you to keep in mind that building 1 hardware device is far too different from building 100.
This is going to be our last post of 2020, we wish you a Merry Christmas and a happy and safe 2021. Thanks everyone for staying with us during this rough year!